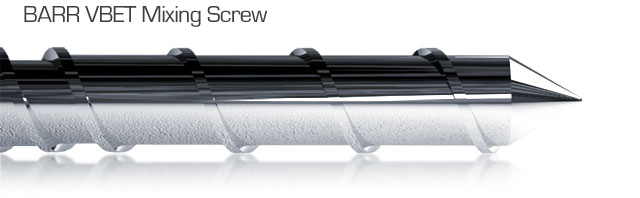
Leading the Competition
The VBET screw channel is divided into two sub-channels. The particles continuously change their position as they flow from one sub-channel into another sub-channel along the screw. A particle in the surface layer of one sub-channel ends up in the center layer of the other sub-channel. This Solid/Melt Flow mechanism gives uniform melt quality and uniform melt temperature by continuously mixing the melt. Undesirable hot spots inside the screw channel are eliminated.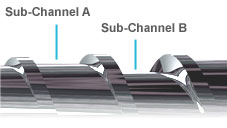
Conduction is the key to the BARR VBET.
The VBET's new low-shear design uses almost half of its length as an Energy Trasfer section, which provides an increase in conductive melting by almost 30%. The VBET Energy Transfer section melts 30-50% of the polymer, eliminating the need for downstream cooling. This not only reduces heat loss, but also, allows a much lower melt temperature. Lower melt temperatures, in turn, mean the processor can facilitate higher maximum rates.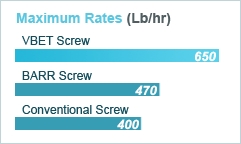
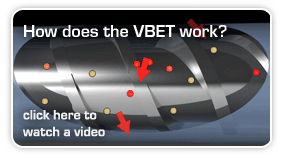
The VBET Difference
Not only has the VBET improved upon the strength of the BARR ET Screw, it incorporates more of the processing power. The Mixing/Melting Section fo the VBET Screw is 30% to 50% longer than the ET Screw.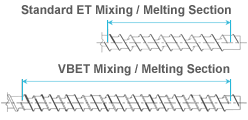
Typical Barrier Screw |
VBET Screw |
Largely keeps
unmelted and melted resin separated
90% of polymer
melted through
shearing
Melt film thickness
in barrier section is
very small
Requires downstream
cooling due to high
temperatures
Both pellets and melt
cross between
channels to increase
conductive melting
30 - 50% of polymer
melted through
conduction
Hot melt flows from
one sub-channel into
another
Conductive heat
transfer elminates
need for downstream
cooling